News
Optimising financial and environmental gains with at source drilling waste management
Water-based and non-aqueous drilling fluids (NAF) and associated drill cuttings are the largest waste streams generated from global offshore drilling operations.
21 November 2019
Published in Offshore Magazine, October 2019
By Andrew Morris, Gareth Innes, Adrian Clark, Pierre-Marie Hinden, TWMA and Laurie Philips AGR Well Management
Water-based and non-aqueous drilling fluids (NAF) and associated drill cuttings are the largest waste streams generated from global offshore drilling operations. Traditionally, the ‘skip and ship’ method is used to collect, contain and transfer waste via vessel to a specialist processing facility onshore.
An alternative and increasingly attractive option, both financially and environmentally, is rig- based thermal processing through the TCC RotoMill®. This utilises frictional based thermal desorption technology at source to separate NAF, debris and associated materials into their three constituent parts of oil, water and solids for recycling, reuse and safe disposal.
In 2018, drilling waste specialist TWMA, was contracted by the licence operator to mobilize drilling waste management services using offshore thermal processing for the 17½” and 12¼” Orlando production well drilling campaign in the UKCS. Managed by well operator, AGR Well Management (AGR) using the Ocean Guardian semi-submersible drilling rig, the contract also included skip and ship services for the 8½” section, due to operational requirements.
Rig-based drilling waste management
Located in block 3/3b in the northern North Sea, the Orlando field is more than 380km (24-hours sailing time) from Aberdeen’s coastline facilities.
Due to the subsea infrastructure being installed shortly after the well was completed and suspended, drill cuttings and other debris had to be collected, removed and disposed of within a tight drilling window. With a total depth of 18,266ft to be drilled in the single subsea well, more than 1,600Mt of drilling waste was anticipated from the three sections.
Treating materials at source with thermal processing technology eliminates the requirement to transport waste long distances onshore via the ‘skip and ship’ method.
The process uses heat generated from kinetic energy to separate the three constituent parts of NAF and remove oil content. Using a hydraulically operated positive displacement piston pump, a cylindrical mill within the unit chamber grinds a bed of solids to generate power.
At a pre-determined temperature, NAF and drill cuttings are fed into the chamber causing the liquids (oil and water) to flash evaporate from the solids. The resulting gases then exit the mill and pass through a cyclone, where any fine solid particles are removed prior to gases travelling to the oil and steam condensers, respectively.
As the goal of the oil condenser is to recover the oil from the gases without condensing the water, the gases are cooled to approximately 105oC. Here, only the oil is condensed whilst the remaining gases containing water will pass through to the steam condenser. By further reducing the temperature to 40oC, the steam condenser will fully shrink the remaining gases. An integrated gravity separator then isolates any remaining light oil fractions to ensures this is removed from the recovered water phase.
Recovered base oil, which retains its full original quality, can be reintroduced to the drilling mud system, representing significant cost savings for operators. Recovered water and solids can be safely dispersed on location as they are well within with UK standards outlined in the Chemical Usage and Discharge permits issued by the Department of Business, Energy & Industrial Strategy and the Scottish Environmental Protection Agency (SEPA).
Thermal process versus ‘skip and ship’
There is a perception that mobilizing thermal processing equipment offshore on a one-well basis would entail high installation costs and involve installation and demobilizing around other drilling related activities. However, following a thorough evaluation of both methods, AGR found significant HSE and operational benefits:
- a reduction in skip handling
- a reduction in waste handling
- reduced weather exposure, i.e. limiting movement of skips on deck and to a dedicated vessel
- a reduction in the requirement for crane use
- no requirement for a dedicated vessel to be at the rig site during drilling
- the ability to re-use base oil in the drilling fluid at source
AGR also undertook a commercial evaluation. Considering the reduction in time waiting on weather, removing the dedicated vessel requirement, and the reduction in logistics costs, it found that, even with the increased rental and mobilization costs, the overall costs could be 36% lower.
Reduced risk, cost and harm to the environment
Despite reduced crane availability, due to weather and other rig mobilization requirements, the offshore thermal processing package was fully installed within nine days, half a day ahead of schedule.
As space was limited on the Ocean Guardian, the thermal processing equipment configuration and layout design was the most compact installation performed to date. Having all the equipment within the same area in a smaller footprint allowed TWMA to achieve the most efficient processing.
More than 1,600MT Mt drill cuttings were processed from the three sections of the Orlando development well: equivalent to 300 skips. This meant:
- a total of 1255.19Mt of recovered solids were diverted from landfill and discharged overboard with an average total petroleum hydrocarbon organics (TPH) of 0.058%, well below the North Sea allowable discharge of <1%
a total of 223.37m3 of recovered water was discharged overboard with an average oil on water of 2ppm, also well below the North Sea allowable discharge of <30ppm.
By processing drill cuttings offshore at source, it was estimated that approximately 26 hours of weather downtime was removed during drilling operations, which would have resulted in an associated spread rate cost of approximately USD380,000.
Consequently, this allowed continuous drilling during adverse weather conditions. It also significantly lowered handling, storage, offshore lifting and ‘skip and ship’ vessel requirements, saving an estimated USD640,000 in vessel costs alone (based on the market rates at that time). Having the package onboard also gave the client flexibility leading to compressed schedules.
In addition, the solution minimized the HSE risks associated with the unloading and offloading of 300 skips, including more than 3,000 associated crane lifts, at the rig site, quayside and ultimately, the processing facility.
The drilling waste management operation was completed within time and on budget with zero Lost Time Incidents and zero loss of containment to the environment during operations.
Summary
The offshore thermal desorption unit performs at processing speeds of up to 10Mt per hour in even the harshest offshore environments and reduces heavy labour lifting operations by up to 95%. Compared with the traditional ‘skip and ship’ method, it also delivers significant cost savings of up to 40% per well. Most notably, it can cut carbon footprint by more than half.
The first single well operation on the Orlando field has proven that onsite thermal processing can safely increase operational efficiency, support well cost reduction initiatives, exceed regulatory requirements and mitigate the likelihood of safety and environmental incidents.
TWMA has since secured five offshore processing contracts with the TCC RotoMill in the UKCS total more than USD20 million. These awards demonstrate the markets outlook at utilising offshore thermal processing technology and further validates the value this technology brings to our client’s operation both in safety, operationally and commercially.
Link to article: https://digital.offshore-mag.com/offshoremag/201910/MobilePagedReplica.action?utm_source=newsletter&utm_medium=email&utm_campaign=TXOFFS191006002&pm=1&folio=50#pg52
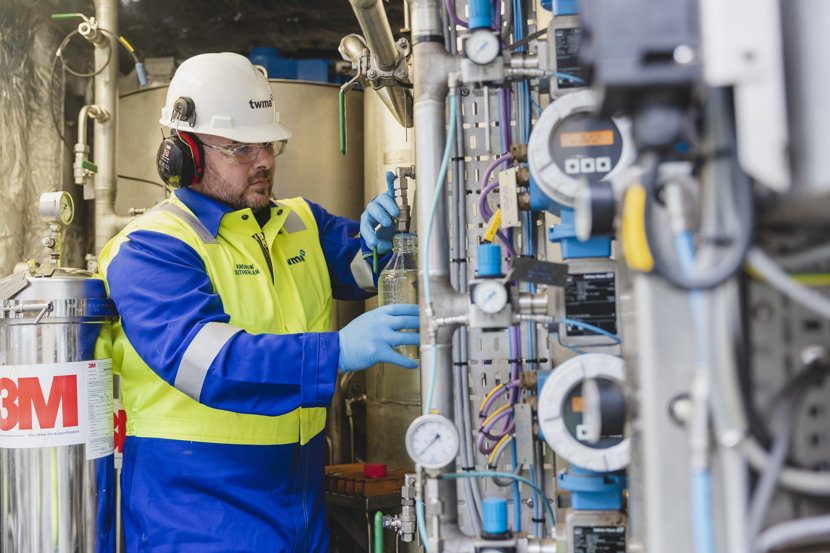
All the latest from TWMA
View all news
All the latest from TWMA
-
News
Meet the TWMA Team.
Want to learn more about life at TWMA in Norway? Discover how our strong partnerships with clients are helping deliver record-breaking drilling performance in Kristin’s recent Q&A:
05 June 2025 -
News
TWMA Secures Major Contract with bp in the UK North Sea.
Drilling waste management specialist, TWMA, has been awarded a contract with bp to provide drilling waste management services in the UK North Sea. This agreement reinforces TWMA’s position as a trusted provider of innovative solutions to the global energy industry.
12 May 2025 -
News
TWMA Celebrates 10 Years LTI-Free at Tullos Materials Management Centre.
Drilling waste management specialist, TWMA, is proud to announce a significant safety milestone, 10 years without a Lost Time Incident (LTI) at its Tullos Materials Management Centre.
25 April 2025 -
News
TWMA Secures Three-Year Contract with TotalEnergies.
Specialist drilling waste management company, TWMA, has secured a three-year contract with TotalEnergies UK for its renowned drilling waste management services, marking the continuation of a long-term relationship between the two companies.
01 April 2025 -
News
TWMA to Share Green Transition Strategies at SPE/IADC International Drilling Conference and Exhibition.
Specialist drilling waste management company TWMA is set to participate in the upcoming SPE/IADC International Drilling Conference and Exhibition.
04 March 2025 -
News
TWMA announces Fourth Quarter Revenue of $18 million.
Specialist drilling waste management company, TWMA, has published its Fourth Quarter results for 2024, with revenue of $18m and EBITDA of $5m.
27 February 2025 -
News
TWMA Breaks Ground on Unrivalled Drilling Waste Management Facility.
TWMA, a global leader in drilling waste management, has officially broken ground on its latest facility in Habshan, Abu Dhabi.
26 February 2025 -
News
TWMA Partners with Multinational Operator for Inaugural Exploration Project in Egypt.
Drilling waste management specialist, TWMA, has announced a landmark partnership with a multinational energy operator for its inaugural exploration project in Egypt.
18 February 2025 -
News
TWMA’s Regional Impact Recognised in Prestigious Awards.
Offshore drilling waste management specialist, TWMA Middle East Limited, has been announced as a finalist in the 2025 Oil & Gas Middle East Awards.
30 January 2025 -
News
TWMA Celebrates 5 Years in the North Sea Without Lost Time Incident (LTI).
Drilling waste management specialist, TWMA, is proud to announce the remarkable achievement of 5 years without a Lost Time Incident (LTI) across its North Sea operations.
10 January 2025 -
News
Sustainable Drilling Waste Solutions Recognised in Prestigious Industry Awards.
Specialist drilling waste management company, TWMA, has been announced as a finalist in this year’s SPE Offshore Achievement Awards.
10 January 2025 -
News
Meet the TWMA Team.
Princy Rajan shares her valuable insights and wealth of experience in a recent Q&A:
13 December 2024 -
News
TWMA Appoints New Group Commercial Director to Drive International Growth.
Specialist drilling waste management compnay, TWMA, has announced the appointment of Jonathan Parkes as its new Group Commercial Director.
09 December 2024 -
News
TWMA named as Driving Sustainability Finalist for 2025 Northern Star Business Awards.
TWMA has been shortlisted for the Driving Sustainability Award at the 2025 Northern Star Business Awards.
05 December 2024 -
News
TWMA announces Q3 revenue of $18million
Specialist drilling waste management company, TWMA, has reported its third quarter 2024 revenue of $18million and an EBITDA for continuing operations of $4.9million.
28 November 2024 -
News
TWMA Expands Middle East Operations Following $70 Million Contract Win.
Specialist drilling waste management company, TWMA, has announced a significant contract win with a leading UAE operator.
30 October 2024 -
News
Meet the TWMA Team.
Pierre-Marie Hinden shares his valuable insights and wealth of experience in a recent Q&A:
18 October 2024 -
News
TWMA Opens New Office in Cairo, Egypt.
TWMA is pleased to announce the opening of its new office in Cairo, Egypt, further solidifying our presence in the country and reinforcing our commitment to the MENA region.
03 October 2024 -
News
Meet the TWMA Team.
Ryan Bowron shares his valuable insights and wealth of experience in a recent Q&A:
10 September 2024 -
News
TWMA to Showcase Innovations at Pareto Securities' 31st Annual Energy Conference.
05 September 2024 -
News
TWMA Announces Second-Quarter Profit of $4.9million.
Specialist drilling waste management company, TWMA, has posted its second quarter 2024 earnings of $19.5million and operating profit of $4.9million.
02 September 2024 -
News
TWMA Secures Contract Extension with Equinor.
TWMA has successfully secured the first of five available contract extensions with Equinor, a major development that could extend their collaborative efforts until May 31, 2034.
13 June 2024 -
News
TWMA Announces Continued Growth with First-Quarter 2024 Results.
Specialist drilling waste management company, TWMA, has posted its first quarter 2024 earnings of $18.3million and EBITDA of $4.7million.
31 May 2024 -
News
TWMA Announces Strong Growth Following Annual Results.
TWMA posted its annual results (year ended to December 31, 2023) reporting an increase in turnover to $70.9million from $67.8million.
20 May 2024 -
News
TWMA Celebrate Award Success for Global Impact.
Drilling waste management specialist, TWMA, has been announced as this year’s Going Global winner at the prestigious Northern Star Business Awards.
22 April 2024 -
News
TWMA Announces Closing of $62.5 Million Sustainability Linked Bond.
Specialist drilling waste management company, TWMA, announced that it has closed on a $62.5 million Sustainability Linked Bond on the Nordic ABM in Oslo.
13 February 2024 -
News
Middle East Award Nomination for RotoMill Technology.
Specialist drilling waste management company, TWMA, has been announced as a finalist in the prestigious Oil and Gas Middle East Awards for its latest generation of RotoMill technology.
06 February 2024 -
News
TWMA named as Going Global Finalist for 2024 Northern Star Business Awards.
Specialist drilling waste management company, TWMA, has been shortlisted for the Going Global Award at the 2024 Northern Star Business Awards.
22 November 2023 -
News
TWMA to double Middle East operations following $100 million contract win.
Specialist drilling waste management company TWMA has secured a $100 million contract for a major sour gas development in Abu Dhabi.
03 October 2023 -
News
Join the Specialists at ADIPEC.
Join TWMA at ADIPEC in hall 8 on stand #8410 from 2-5 October in Abu Dhabi.
28 September 2023 -
News
TWMA secures major contract with Norwegian giant Equinor.
20 September 2023 -
News
TWMA to present innovations at Pareto Securities' 30th Annual Energy Conference.
19 September 2023 -
News
TWMA launches RotoMill 2.0 wellsite processing solution.
07 September 2023 -
News
TWMA secures bp Egypt contract worth $15 million.
TWMA has been awarded a contract worth up to $15 million to support a large-scale oil and gas project for bp in Egypt.
14 August 2023 -
News
TWMA Middle East celebrates milestone of 5 million work hours without lost time incident (LTI).
TWMA, the specialist drilling waste management company, has achieved 5 million work hours lost time incident (LTI) free across its Middle East operations.
02 August 2023 -
News
TWMA decarbonisation efforts recognised with win at Offshore Achievement Awards.
TWMA, the drilling waste management specialist, received the Carbon Reduction in Conventional Assets award at the 2023 Offshore Achievement Awards.
20 March 2023 -
News
TWMA secures seven-figure contract with North Sea operator.
Specialist drilling waste management company, TWMA, has secured a seven-figure contract with a major North Sea oil and gas operator.
02 March 2023 -
News
TWMA celebrates reaching 4.5 million work hours LTI free in the Middle East.
TWMA, the specialist drilling waste management company, has achieved 4.5 million work hours lost time incident (LTI) free across its Middle East operations.
02 February 2023 -
News
TWMA named as Carbon Reduction in Conventional Assets finalist for 2023 SPE Offshore Achievement Awards.
Specialist drilling waste management company, TWMA, has been shortlisted for the Carbon Reduction in Conventional Assets Award at this year’s SPE Offshore Achievement Awards.
18 January 2023 -
News
TWMA launches XLink™ real time monitoring and automation solution at ONS.
TWMA, has launched its new XLink™ solution, designed to provide oil and gas operators with increased automation, deeper insights and real time data monitoring to improve the efficiency of their wellsite drill cuttings processing system
31 August 2022 -
News
Drill Cuttings Treatment Alternatives - A Comparative Emissions Assessment.
A case study assessing the CO2 footprint and NO2 emissions for different drill cuttings treatment alternatives.
02 February 2022 -
News
TWMA reaches key UAE milestone as it achieves API Q2 Certification.
Specialist drilling waste management company TWMA has secured the American Petroleum Institute (API) Q2 accreditation for its UAE operation, the first quality management system (QMS) certification for service suppliers in the oil and gas industry.
18 January 2022 -
News
Case Study: A wellsite processing solution proven to lower carbon emissions.
Specialist drilling waste management company TWMA highlights how its wellsite processing solution has been proven to reduce the carbon emissions of oil and gas drilling operations by 50%.
10 January 2022 -
News
TWMA’s wellsite processing solution proven to reduce carbon emissions of drilling operations by 50%.
Specialist drilling waste management company, TWMA, will highlight how its wellsite processing solution has been proven to reduce the carbon emissions of drilling operations by 50% at this year’s ADIPEC.
16 November 2021 -
News
TWMA Celebrates 20 Years of Offshore Processing.
TWMA celebrates 20 years of offshore processing, delivering the gold standard in wellsite technology application and operational excellence.
15 July 2021 -
News
TWMA awarded three-year extension for Aker BP's Valhall Flank Project.
TWMA, the specialist drilling waste management company, has been awarded a three-year contract extension to supply integrated waste management services for Aker BP’s Valhall Flank North and Hod B field development projects on the Norwegian Continental Shelf (NCS).
16 June 2021 -
News
TWMA Named as Net Zero Award Finalist for SPE Offshore Achievement Awards.
Specialist drilling waste management company, TWMA, has been shortlisted in the Net Zero category at this year’s SPE Offshore Achievement Awards.
06 May 2021 -
News
TWMA secures first contract with Spirit Energy at Grove field.
Specialist drilling waste management company, TWMA, has secured a seven-figure contract with leading exploration and production company, Spirit Energy.
25 February 2021 -
News
TWMA’s move to new global HQ in Aberdeen to support growth plans and new technology roll outs.
Specialist drilling waste management company, TWMA, has secured new headquarters in Aberdeen to support business growth and deliver remote operations for its customers.
04 February 2021 -
News
North east classrooms refreshed and charities uplifted by TWMA’s office donations
TWMA has used an office upgrade as an opportunity to uplift local schools and charities.
03 December 2020 -
News
Drill into the low carbon benefits of processing at source
31 August 2020 -
News
TWMA reaches 9 years LTI free operations in Egypt
Drilling waste specialist, TWMA, has reached the milestone of nine years Lost Time Incident (LTI) free operations in Egypt across its sites in Cairo and Alexandria.
11 May 2020 -
News
TWMA adapts equipment to provide critical service to major operator in UAE
Drilling waste specialist, TWMA, has adapted its onsite drilling waste handling equipment to support safe operations for a major operator as it manages through the current crisis.
29 April 2020 -
News
The benefits of processing drill cuttings at the rig site
When it comes to defining the methodology for drill cuttings treatment, it is now possible to materially reduce costs, improve safety, and lower the carbon emissions of drilling projects.
19 March 2020 -
News
TWMA appoints new CEO
Specialist drilling waste management company, TWMA, has announced the appointment of Halle Aslaksen as its new CEO.
19 February 2020 -
News
Optimising financial and environmental gains with at source drilling waste management
Water-based and non-aqueous drilling fluids (NAF) and associated drill cuttings are the largest waste streams generated from global offshore drilling operations.
21 November 2019 -
News
TWMA secures £20 million of North Sea contracts
Specialist drilling waste management company, TWMA, has secured new contracts valued at £20 million in the North Sea in the first eight months of 2019.
04 September 2019 -
News
TWMA achieves 12 months LTI free
Specialist drilling waste management company, TWMA, has reached 12 months lost time incident (LTI) free operations.
27 June 2019 -
News
TWMA named as Great Company (Large) at 2019 Offshore Achievement Awards
TWMA, provider of specialised drilling waste management services, has won the Great Company (Large) Award at this year’s Society of Petroleum Engineers (SPE) Offshore Achievement Awards (OAA).
22 March 2019 -
News
TWMA Maintains Growth Strategy, Acquires US Service Company
TWMA, provider of specialised drilling waste management services, has announced its acquisition of US-based Dynamic Oilfield Services in an eight-figure deal.
20 June 2018